Processing Rooms: definition and guidelines
Processing Rooms: definition
A processing room in a food environment is an area dedicated to the preparation, handling, and processing of food products, where it is essential to ensure high standards of hygiene and food safety.
These places must be designed with particular attention to avoid food contamination and ensure a safe working environment for the personnel involved.
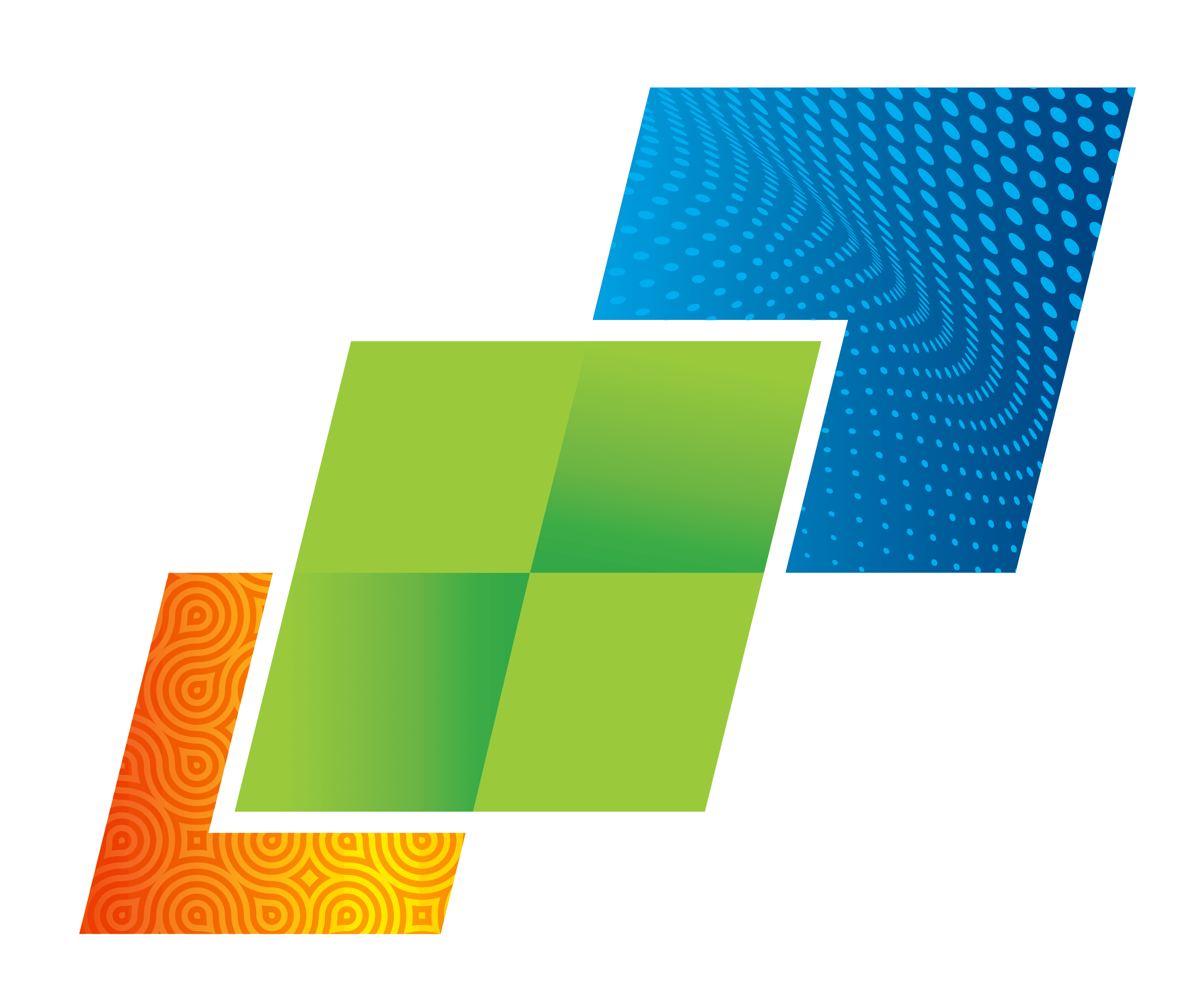
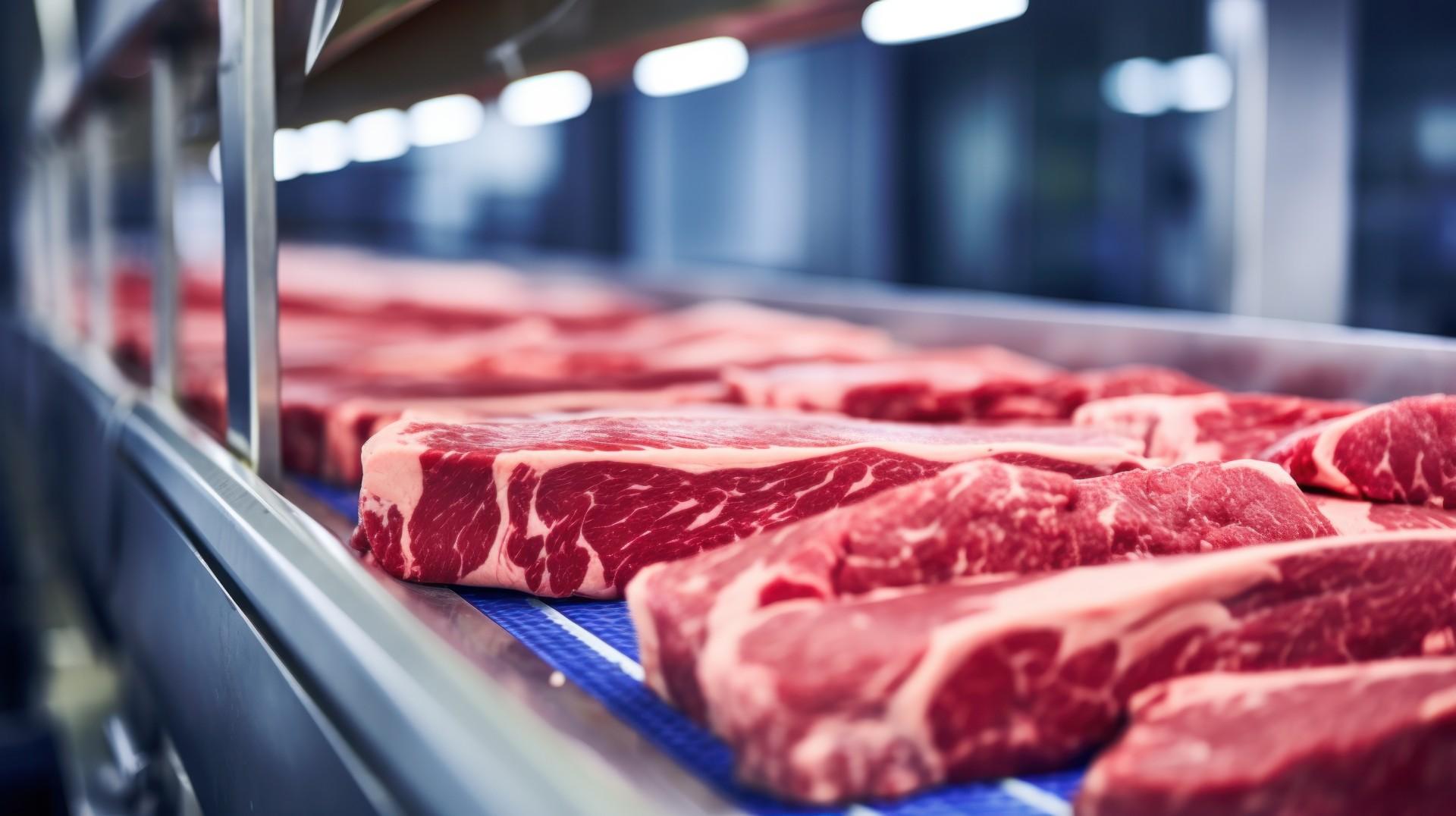
Requirements for Processing Rooms
In the context of a food environment, hygiene is of paramount importance, which implies the need to subject the room to frequent and thorough cleaning processes. These environments must therefore be designed with materials that resist humid and aggressive environments, avoiding the formation of rust and mold. Sandwich panels used for walls and ceilings must be made of materials that meet high standards of moisture resistance, corrosion resistance, and microbiological contamination.
The design of the room should facilitate the regular cleaning and disinfection of all surfaces and tools used during the food processing process. This includes the selection of smooth, non-porous, and easy-to-clean materials, such as fiberglass.
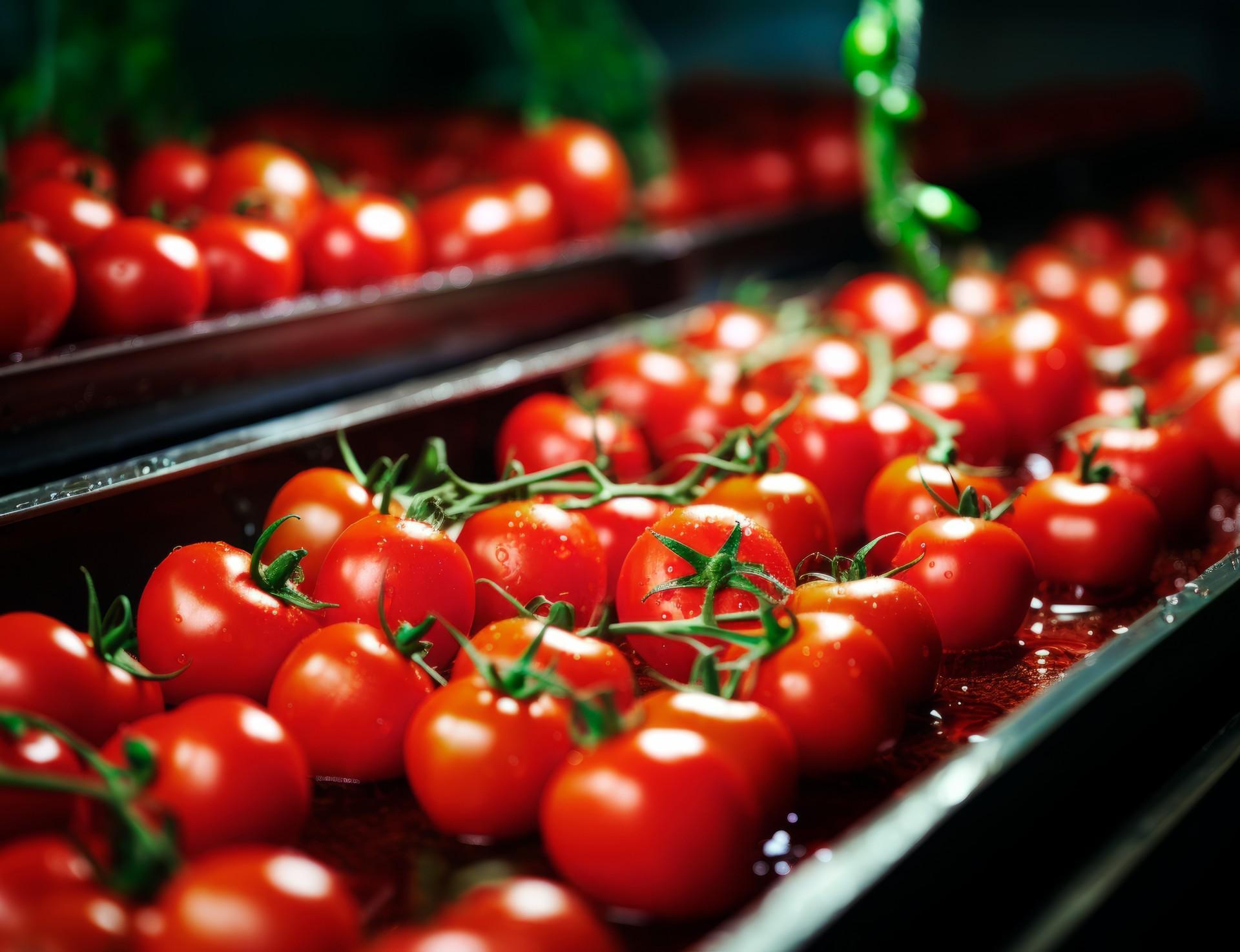
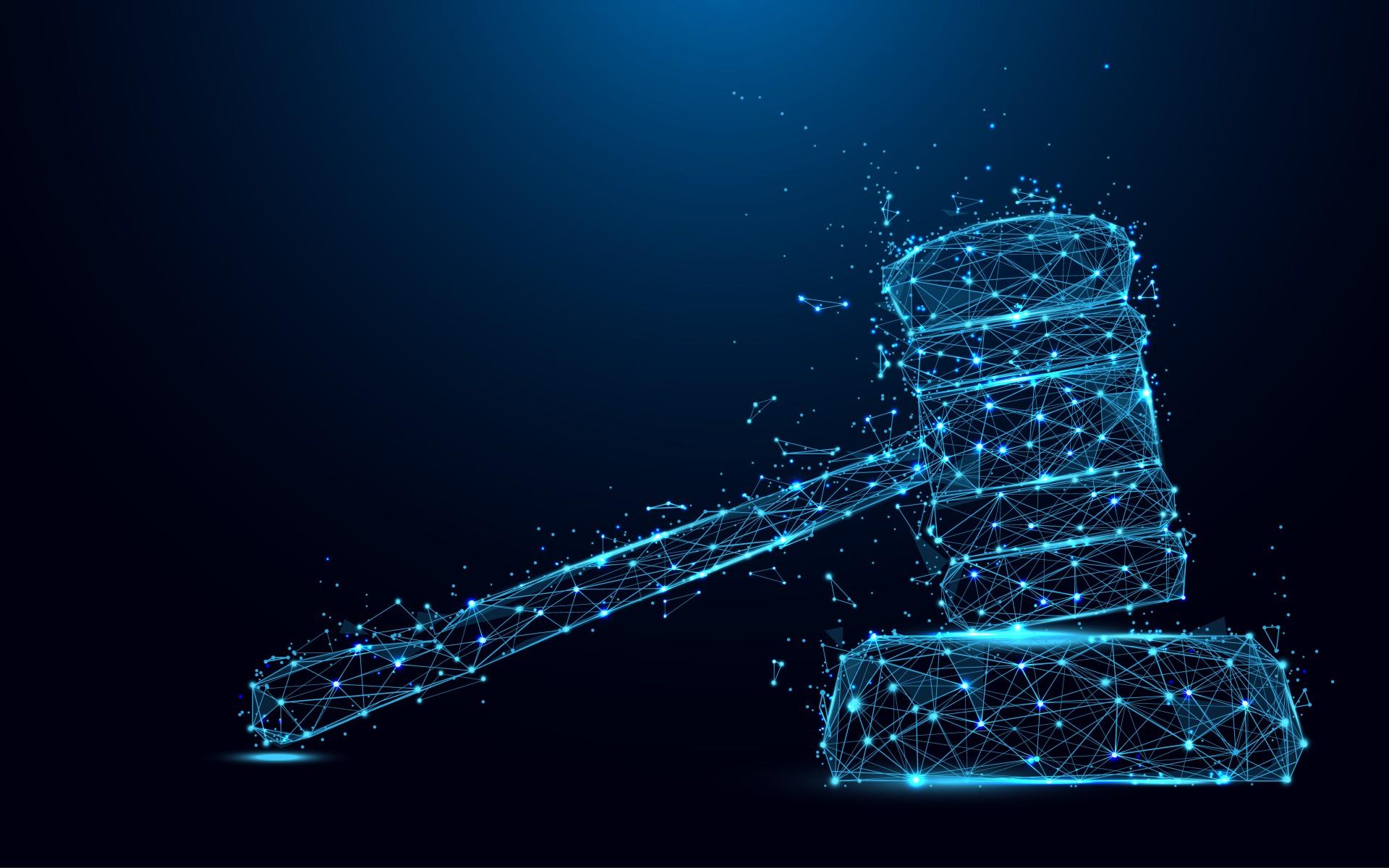
Guidelines for Processing Rooms
At the European level, the EN 1672-2:2005 standard is followed, which provides detailed guidelines for the hygienic design of food equipment, including the walls and ceilings of environments where food is processed.
Another important regulatory reference is EN 12463-1:2002 which deals with the general performance of industrial doors, including doors for food processing environments.
Why Invest in Processing Rooms
The crucial importance of a food processing room lies in its ability to ensure impeccable hygienic conditions for the safe and high-quality production of food.
The choice of materials for walls and ceilings is fundamental, as the formation of rust or mold can compromise not only the health of the food but also the operational efficiency of the facility. Any corrective action in case of material deterioration not only entails significant costs but often also implies plant downtime. This interruption can cause considerable economic losses, from production cessation to the risk of having to dispose of contaminated products.
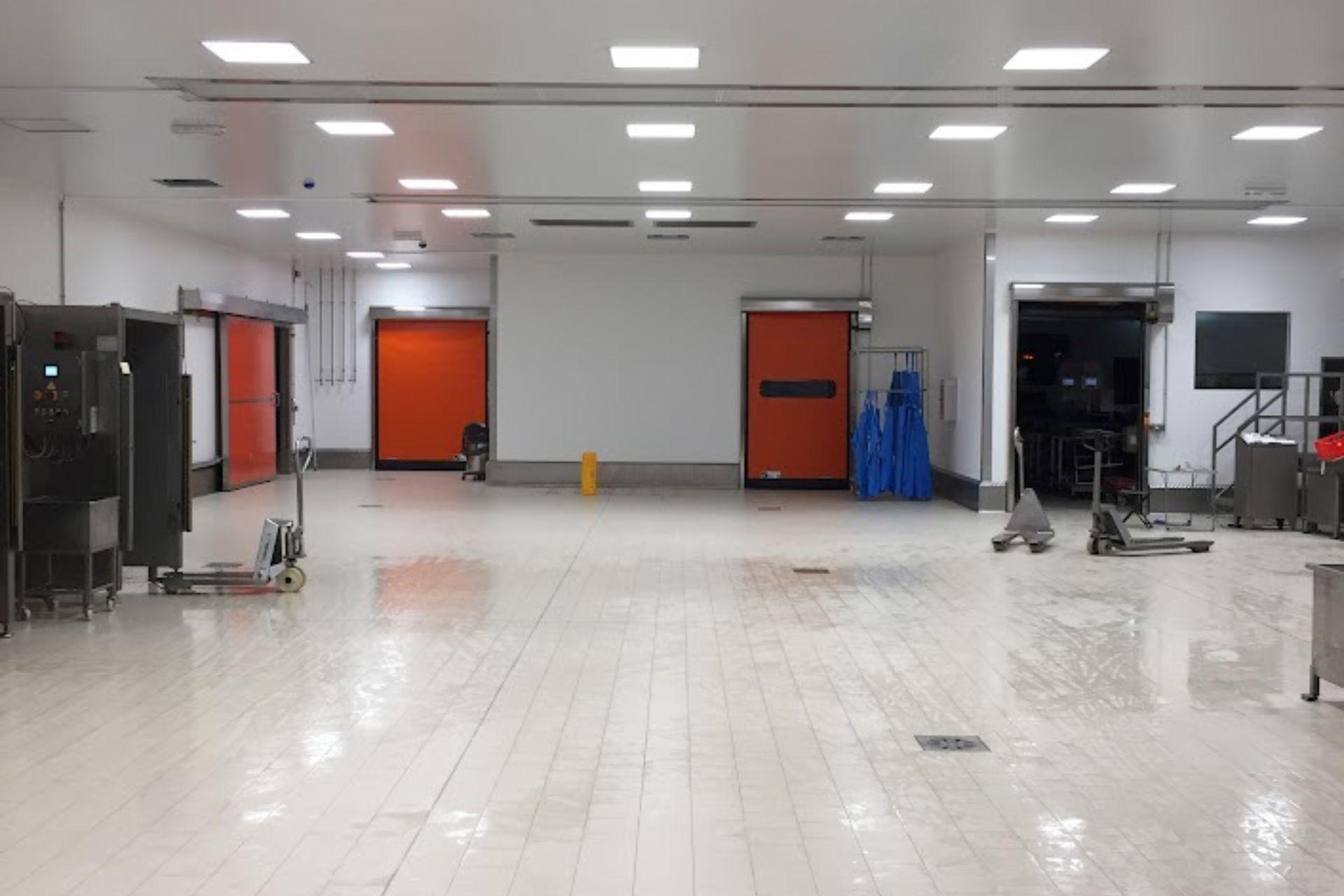